Как точно выставить тиски на столе станка?
Довольно часто на установку машинных тисков не обращают никакого внимания. Тиски устанавливают на столе станка, как попало, что приводит к возникновению различных трудностей во время обработки, а в некоторых случаях и к неисправимому браку. Точная установка тисков позволяет вести обработку деталей без дополнительных проблем и обеспечить высокое качество обработки.
Лучше всего проверку положения тисков, как в продольном, так и в поперечном направлении, выполнить с помощью индикаторной головки. Для этого в шпиндель или суппорт станка (если станок строгальный или долбёжный) устанавливается оправка, к которой крепится индикаторная головка. Первоначально при установке тисков необходимо убедиться в том, что базовые направляющие тисков параллельны плоскости стола станка.
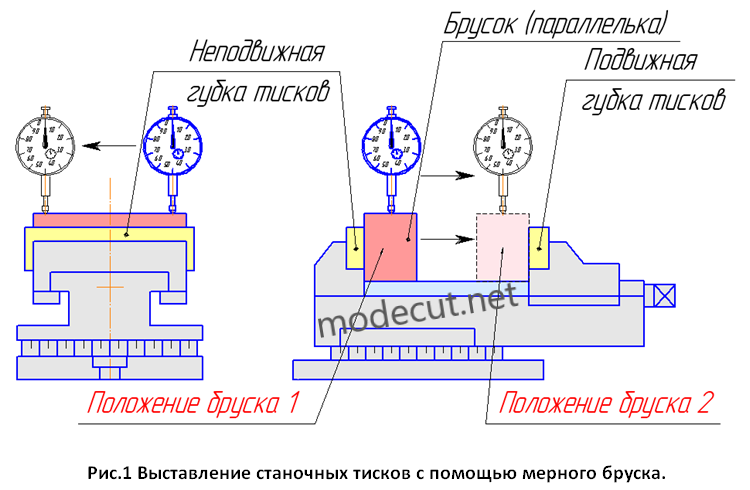
Для этого подвижную губку тисков отводят как можно дальше, а на направляющие тисков устанавливают точный брусок (см. рис.1). Как видно из рисунка изначально брусок устанавливается вплотную к неподвижной губке. Затем перемещая стол станка, к одному из концов бруска подводят индикаторную головку, таким образом, чтобы её наконечник с небольшим натягом (около 0,2мм), коснулся поверхности бруска. Далее перемещают стол так, чтобы наконечник индикатора оказался на другом конце бруска. При этом во время перемещения стола наблюдают показания индикатора. Если отклонение стрелки индикатора будет не более 0,02мм, то считается, что направляющие тисков в заданном горизонтальном направлении параллельны плоскости стола. Затем такую проверку проводят и в другом горизонтальном направлении. В этом случае предварительно запоминают текущее значение индикатора возле неподвижной губки и затем сдвигают мерный брусок к подвижной губке тисков.
Далее не меняя положения индикатора по высоте, перемещают стол станка до тех пор, пока наконечник не наедет на поверхность мерного бруска (см. рис.1). Разность показаний индикатора возле подвижной и неподвижной губки и есть отклонение от параллельности направляющих тисков в этой плоскости. Здесь допустимое отклонение от параллельности также должно быть не более 0,02мм.