В чем отличия между плазменной и газовой резкой?
(Страница 2)
К недостаткам кислородной газовой резки можно отнести следующие факторы: невысокое качество реза, деформация и поверхностное закаливание отрезаемых деталей, ограничение резки по обрабатываемым материалам. Невысокое качество резки, отображается не равномерностью ширины реза, наличием косины и большой шероховатости на срезанной кромке, а также присутствие подплавлений и небольшого грата. Что качается ограничений по материалам, то газовая резка в основном применяется для резки сталей с содержанием углерода до 0,4% С. Резка углеродистых сталей с содержанием углерода больше 0,4%, приводит к образованию на боковых сторонах заготовки поверхностной закалки, что усложняет последующую механическую обработку. Довольно плохо поддаются резке высокоуглеродистые инструментальные стали. Это связано с тем, что температура плавления высокоуглеродистых сталей близка к температуре воспламенения.
Вследствие чего при резании окалина не будет выдуваться из зоны резания, а будет смешиваться с расплавленным металлом, расположенным на краю резания. Из-за формы своих зерен и наличия графита в своей структуре совсем не режется чугун (за исключением ковкого чугуна). Также по причине низкой температуры плавления, совсем не поддаются кислородной резке алюминий, медь и их сплавы.
Плазменная резка – это термический процесс резания материалов, который выполняется плазменной струёй. При создании плазменной струи, от источника питания подается ток, с помощью которого между электродом (катод), находящимся внутри плазмотрона, и деталью (анод) зажигается электрическая дуга (см. рис.2). Затем в сопло под давлением подается плазменный газ, который с помощью электрической дуги ионизируется и превращается в плазменную струю. В качестве плазменного газа при резке используются активные газы (воздух, кислород), которые окисляют металл и неактивные (азот, аргон). Активные газы применяются при резке черных металлов, а неактивные при резке цветных металлов и сплавов. Срезаемый материал расплавляется и удаляется из зоны резания струёй плазменного газа. Для предохранения сопла и электрода от перегрева плазмотрон оснащен охлаждающими каналами.
Также через дополнительные каналы в зону резания поступает вихревой газ, который обволакивает плазменный поток и способствует улучшению качества резки (см. рис.2). Во время резки вихревой газ сужает плазменный поток и защищает режущее сопло и кромку заготовки от оплавления. В основном в качестве вихревого газа, используют азот или воздух (только при резке черных металлов).
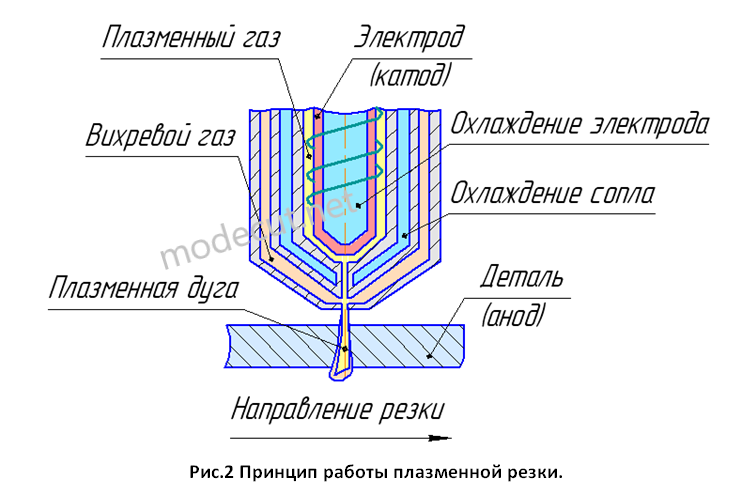
В отличие от кислородно-газовой резки, плазменной резка не зависит от процесса окисления, поэтому она применяется для обработки не только черных, но и цветных металлов и сплавов. Для обеспечения процесса резки нужно, только чтобы разрезаемый материал был токопроводящим. На практике плазменная резка используется для разрезания заготовок толщиной не более 40мм, так как для выполнения резки больших толщин требуется иметь источники питания довольно высокой мощности. При резке небольших толщин металла, за счет более быстрого нагрева скорость резания плазменной резки значительно выше, чем газовой. Однако с увеличением толщины заготовки скорость заметно снижается. Получаемое качество реза, также значительно выше, чем при газовой резке, за счет более равномерной ширины реза, лучшей шероховатости и меньшего количества грата. Также стоит отметить, что процесс плазменной резки является более безопасным, так как при нем не используются горючие газы (пропан, бутан).
Согласно представленной информации можно сделать выводы, что разрезку заготовок из низкоуглеродистых сталей толщиной до 30мм лучше выполнять плазменной резкой. При больших толщинах заготовку выгодней разрезать газовой резкой. Разрезка высокоуглеродистых, а также цветных металлов и сплавов выполняется только плазменной резкой.